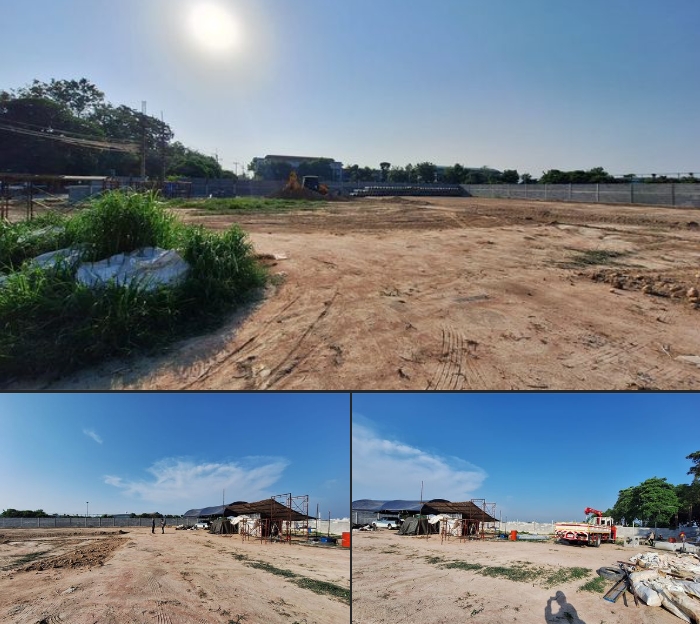
Our workshop coming soon.
We bringing success to your hand.
Our workshop coming soon.
Pile and bore pile we did.SOAGE ENGINEERING .
……………………………….
SOAGE ENGINEERING .
————————-
[CONTACT US ]
TEL :: +66 89 407 3902
EMAIL :: prateep.soage@gmail.com
FB :: SOAGE Engineering CO.,LTD
WEBSITE : : soage.co.th
SEO
#งานระบบท่อทุกชนิด
#งานโครงสร้างเหล็ก
#งานซัพพลายแมนพาวเวอร์
#งานรับเหมาก่อสร้างทุกชนิด
#งานซ่อมบำรุง
#steelstructure
#งานโครงสร้างเหล็ก
#pipework
#งานระบบท่อ
#supplymanpower
#งานซ่อมบำรุง
#maintenance
#equipmentwork
Pipe works.
#งานติดตั้งระบบท่อ#งานโครงสร้าง#งานเชื่อมท่อ#ระบบท่อประปา#งานดักท์#งานซ่อมบำรุง#manpowersupply
ติดต่อสอบถามข้อมูล
ประทีป อุ่นรัมย์
โทร : 0939894593
บริษัท โซเอจเอ็นจิเนียร์ริ่ง จำกัด