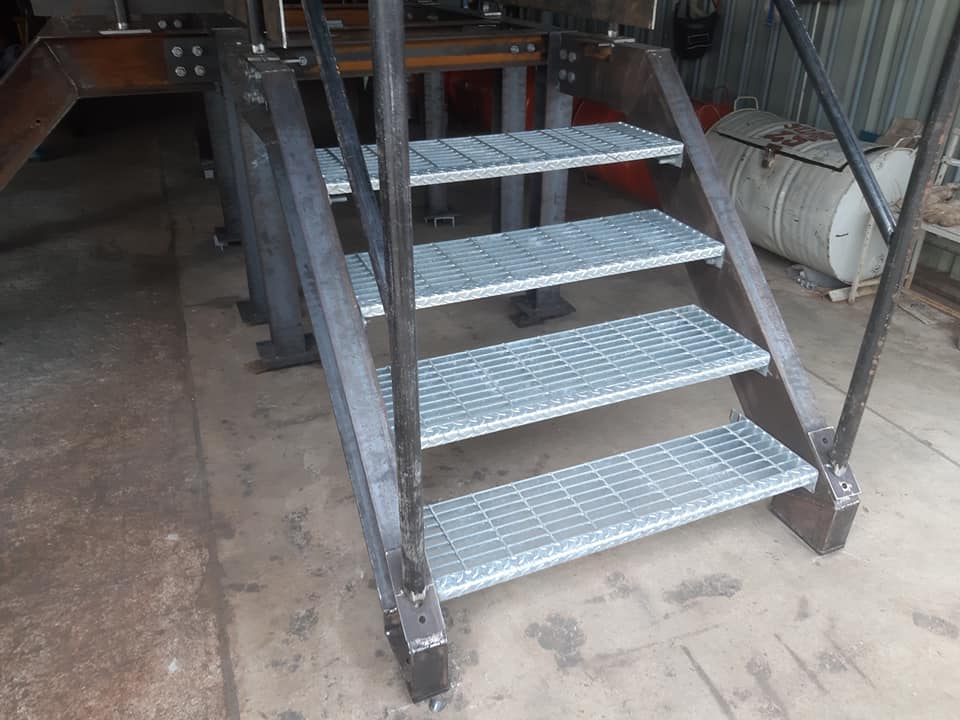
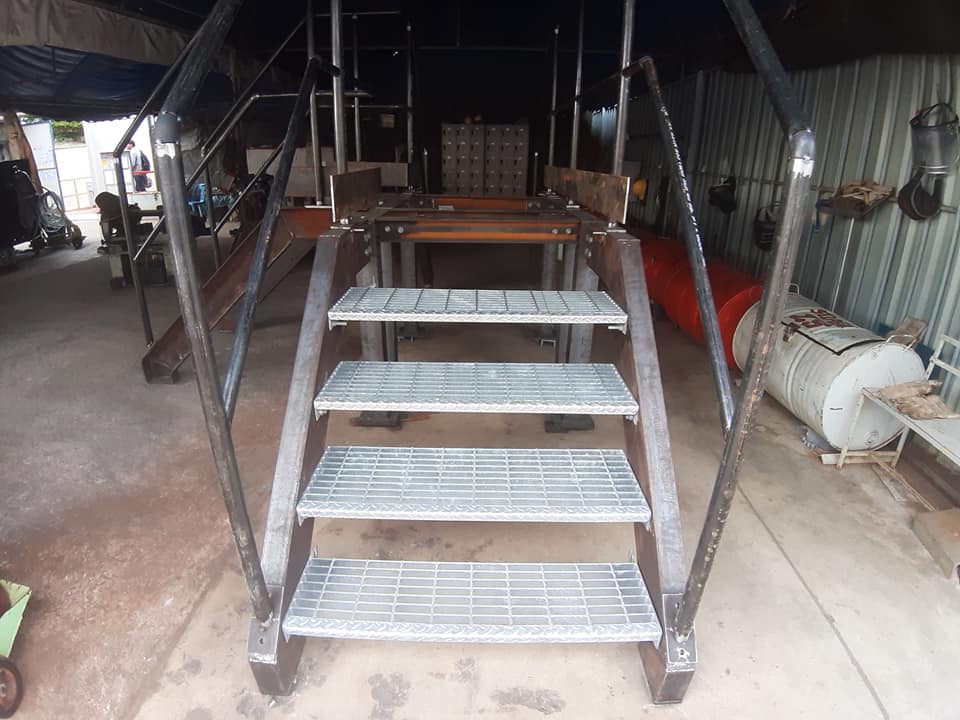
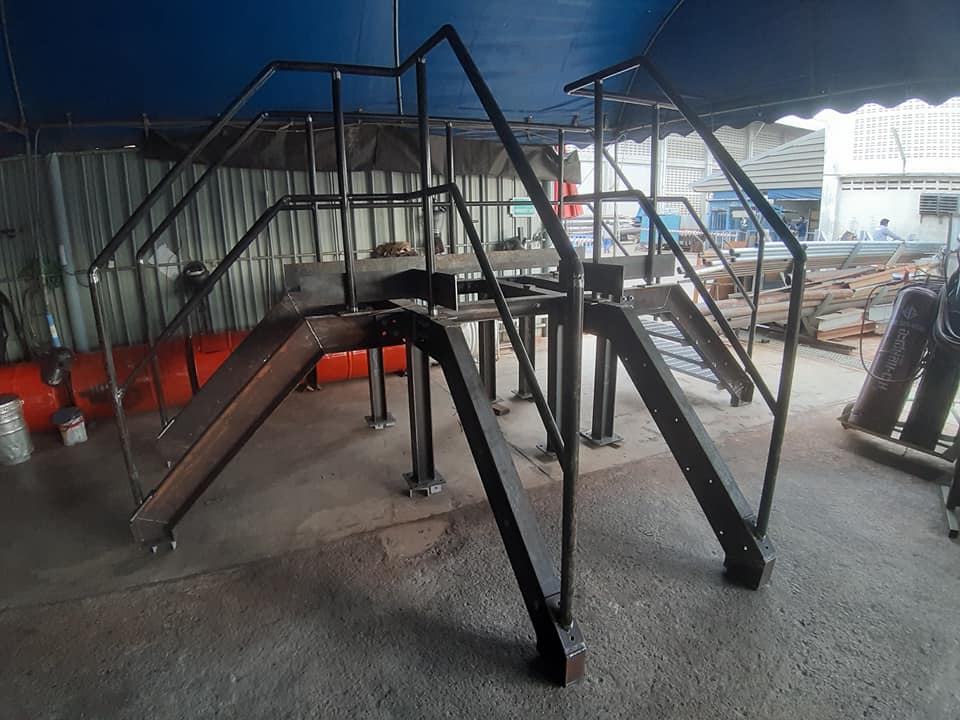
We bringing success to your hand.
Chemical Skid
Chemical Skid
ทีมงาน SOAGE เตรียมความพร้อมสำหรับ การปรับปรุง พัฒนาองค์กร เพื่อเพิ่มความแข็งแกร่ง ของบริษัทฯ
SOAGE เตรียมความพร้อมสำหรับ การปรับปรุง พัฒนาองค์กร
SOAGE เตรียมความพร้อมสำหรับ การปรับปรุง พัฒนาองค์กร
รับ Audit ISO 9001:2008 ในรอบ Surveillance ครั้งที่ 2
รับ Audit ISO 9001:2008 ในรอบ Surveillance ครั้งที่ 2
Futuristic highway repair technologyPlease – LIKE ➡️ iViral – iViralUS.com
โพสต์โดย iViral บน 30 พฤษภาคม 2017
โพสต์โดย Information Civil Engineering บน 26 กรกฎาคม 2015
คำค้นหาเรา : TAG
………………………………………….
EPC,Piping,hvac,steel,structure,equipment,installation,petrochemical,refinery,บำรุงรักษา,เครื่องจักร,รื้อถอน,ขนย้าย,ติดตั้ง,งานเชื่อม,ระบบท่อโรงงาน,thaioil,maptaphut,มาบตาพุด ,ให้บริการบำรุงรักษา,ให้บริการเครื่องจักร,ให้บริการรื้อถอน,ให้บริการขนย้าย,ให้บริการติดตั้ง,ให้บริการงานเชื่อม,ให้บริการระบบท่อโรงงาน,EPC service,Piping service,hvac service,steel service,structure service,equipment service,installation service,petrochemical service,refinery service
เปิดไซต์งานใหม่ Vinythai Public Company Limited Medical Service · Rayong
เปิดไซต์งานใหม่ Vinythai Public Company Limited Medical Service · Rayong
เปิดไซต์งานใหม่ Vinythai Public Company Limited Medical Service · Rayong
AAE Group@Seagate Project : Utility Process Project : Nearly Handover ( www.aae-eng.com )
โพสต์โดย Sompob Boonyai บน 25 พฤษภาคม 2017
ระบบท่อในโรงงาน,อุตสหกรรมท่อสำหรับระบบโรงงาน
A wide range of factories have extensive networks of piping systems carrying hot fluids. Piping configurations may have hundreds of exposed fittings, such as tees, unions, valves, flanges, gauge stations and larger elements such as turbines, tanks and heat exchangers. These industries may include plastics, food processing, petrochemicals, commercial laundries, paper and pulp, metal treatment and many others. Hot pipes and associated fittings may carry steam, condensate, hot water, process fluids or hot manufactured liquid products.
Insulation Deficiencies
In most cases the piping is at least partially insulated, though sometimes even that insulation is inadequate or has become damaged. Commonly though, many fittings are not insulated or were given only an initial wrap or spray insulation treatment. Often that initial insulation was removed when the device first needed service and was not replaced. This may be because qualified personnel from local commercial insulators are not readily available or are perceived to be too costly for small repair jobs. Or it may simply be the perception that frequent access will be needed and insulation will get in the way.
ระบบท่อในโรงงาน,อุตสหกรรมท่อสำหรับระบบโรงงาน
Inadequate insulation on fittings, tanks and other equipment can result in very high energy losses and may cost the plant tens or even hundreds of thousands of dollars annually. Further, exposed hot surfaces can represent a safety hazard to workers and may create excessively noisy or uncomfortable working conditions. With the right insulation, these problems are eliminated. Today, industrial insulation specialists offer custom products that can be fitted to nearly every device and fitting. Custom blanket insulation can be quickly removed for access to the fitting, and can be just as quickly replaced.
Large Field for Improvement
Mellanie Askew represents Coverflex Mfg. Inc., a major industrial insulation manufacturer. According to Askew, removable insulation products are made of various types of fiberglass materials, and can be installed on nearly all fittings and many other problem areas. She comments, “It seems like there is a lot of under-insulated equipment and piping. We estimate that 10-30% of all installed mechanical insulation is either damaged or missing.” This does not include devices that were never insulated in the first place.
She points out that it is often important for insulation blankets to be removable for inspection or service. “Our Coverflex blankets have fastening systems using stainless steel buckles, D-rings and straps, Velcro fasteners or stainless tie wire. All can easily be removed and reinstalled with no special tools.”
Short Payback
for Insulation Investment
Askew notes that insulation additions or repair projects often have paybacks of less than a year. She cites an example of a six-inch steam valve that operates at 350°F and is uninsulated. It has a fuel cost for lost steam energy as high as $880 per year. That same valve if insulated with two inches of high-temperature insulation would reduce the energy lost by 95%, a savings of as much as $800 annually, and a ten-year savings of $8,000.
She adds that in addition to the energy cost savings, adding insulation provides personnel protection, prevents moisture condensation, maintains product termperatures, reduces combustion emissions and adds fire protection. “All of this is in addition to an excellent return on investment.”
The advantages of removable and replaceable insulation are many. Arnold Mazurkiewicz from Shannon Enterprises was a recent presenter at a Technology & Market Assessment Forum sponsored by the Energy Solutions Center. His firm specializes in the installation of Insultech® blanket insulation products.
Access Needed to Fittings
He points out the disadvantages of conventional wrap or spray insulation on industrial pipe fittings. “These are complex surfaces and quick access is needed. Each time conventional insulation is removed, a contractor has to be brought in to replace it.” Further, he explains that conventional insulation may not hold up to field conditions of moisture, temperature or steam leaks. “The end result is a neglected surface condition.”
The solution is custom, removable blanket insulation designed to withstand high temperatures. According to Mazurkiewicz, the typical industrial facility that uses steam has 250 exposed fittings, with an energy loss of $75,000 per year. “The average opportunity for annual savings here is $68,000.” He notes that the typical return on investment ranges from 4 to 14 months. “Remove and reinstall the insulation just once and you are ahead.”
Custom Designed for Each Device
Custom blanket insulation is designed for each specific device, with correct match-up around the valve bonnet, and correct overlap with adjacent pipe or fitting insulation. For installations where there might be condensation or liquid leaks, the insulation usually has a drip grommet so liquid does not accumulate inside the blanket and any leaks can be quickly spotted. Exterior blanket surfaces are often Teflon-coated fabric for easy cleaning and resistance to high temperatures.
Mazurkiewicz and Askew both emphasize the importance of a complete insulation energy appraisal of the industrial facility to determine areas needing attention. The appraisal puts actual dollar savings to Btu losses as well as calculating potential reductions in emissions of greenhouse gases. The appraisal is based on data supplied by the plant or energy manager and gathered during a facility walk-through. This data is fed to a computer program that calculates energy savings on an annual basis.
Infrared Technology Used to Identify Targets
According to Mazurkiewicz, an infrared gun or camera is normally used to obtain surface temperatures and each fitting examined is also tagged for identification. The blanket insulation supplier can then design removable wraps for each fitting. Usually a follow-up infrared survey is done to verify the results of the insulation project.
Gary Orlove is an Application Engineer and Curriculum Manager at the Infrared Training Center of FLIR Systems Inc., a major manufacturer of infrared sensing equipment. He notes that there is widespread acceptance and growing use of infrared systems for determining and measuring the need for insulation in industrial facilities. He points out that interpretation of infrared sensing results must be done by a qualified person. He explains, “If the industrial owner has taken training in use and interpretation of IR images, then he can do this himself, otherwise it is best to use an outside specialist.”
Time to Get Started
With a comprehensive facility review and a program of insulating all pipes and fittings with modern insulating products, major savings in plant energy use are achievable. Further, the facility will be quieter, dryer and safer. If your plant has not done such a systematic insulation review, now is the time. Let the savings begin.